Your Complete Guide to Solvent Recyclers

As awareness around environmental concerns continues to increase worldwide, company’s are increasingly aware of the role they must play.
Unfortunately, companies wishing to be better stewards of the environment quickly discover that the implementation of most solutions to these environmental issues require additional investment in time or resources.
Solvent recyclers are an exception to this. They are a great way for companies to mitigate their environmental footprint, while actually saving money.
A rare win-win situation for both the environment and the firm.
In this guide we are going to explore all of the questions people have when first discovering solvent recyclers including:
As awareness around environmental concerns continue to increase worldwide, company’s are increasingly aware of the role they must play.
Unfortunately, companies wishing to be better stewards of the environment quickly discover that the implementation of most solutions to these environmental issues require additional investment in time or resources.
Solvent recyclers are an exception to this. They are a great way for companies to mitigate their environmental footprint, while actually saving money.
A rare win-win situation for both the environment and the firm.
In this guide we are going to explore all of the questions people have when first discovering solvent recyclers including:
What is a solvent recycler?
Solvent recyclers are machines designed to decontaminate and purify used/dirty industrial solvents so that they can be used again.
Contaminants such as resins, pigments and oils are separated from the solvents and captured to be disposed of through a specific distillation process.
Solvent recyclers function with minimal loss, and are able to recapture up to 95% of used solvents for re-use.
Solvent recyclers come in different sizes and configurations, depending on the solvent used and the volume of solvent used/produced in your specific application.
Solvent recyclers are machines designed to decontaminate and purify used/dirty industrial solvents so that they can be used again.
Contaminants such as resins, pigments and oils are separated from the solvents and captured to be disposed of through a specific distillation process.
Solvent recyclers function with minimal loss, and are able to recapture up to 95% of used solvents for re-use.
Solvent recyclers come in different sizes and configurations, depending on the solvent used and the volume of solvent used/produced in your specific application.
How do solvent recyclers work?
Solvent recycling uses a multi-stage distillation process to separate contaminants from the solvents at temperatures below the solvent’s boiling point.
The separated waste is then collected and disposed of, leaving you with solvent that is as good or better than new.
Solvent recovery process :
- Dirty solvent is fed, automatically or manually depending on equipment, into the distillation tank.
- The distillation vessel is fitted with a thermal oil jacket heated by one or more electric radiators, which bring the used solvent’s temperature close to its boiling point.
- Once the waste has been separated from the solvent, the recovered solvent vapors are conveyed to an air-cooled condenser, where they cooled back to their liquid form.
- The clean liquid solvent is then directed to clean solvent collection drums, where it is ready for reuse.
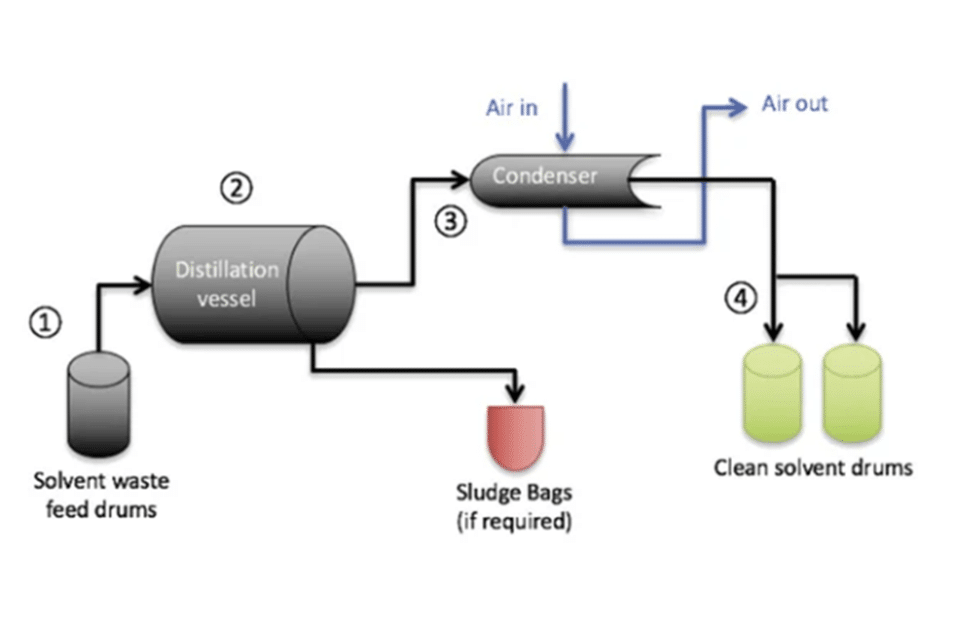
Solvent recycling uses a multi-stage distillation process to separate contaminants from the solvents at temperatures below the solvent’s boiling point.
The separated waste is then collected and disposed of, leaving you with solvent that is as good or better than new.
Solvent recovery process :
- Dirty solvent is fed, automatically or manually depending on equipment, into the distillation tank.
- The distillation vessel is fitted with a thermal oil jacket heated by one or more electric radiators, which bring the used solvent’s temperature close to its boiling point.
- Once the waste has been separated from the solvent, the recovered solvent vapors are conveyed to an air-cooled condenser, where they cooled back to their liquid form.
- The clean liquid solvent is then directed to clean solvent collection drums, where it is ready for reuse.
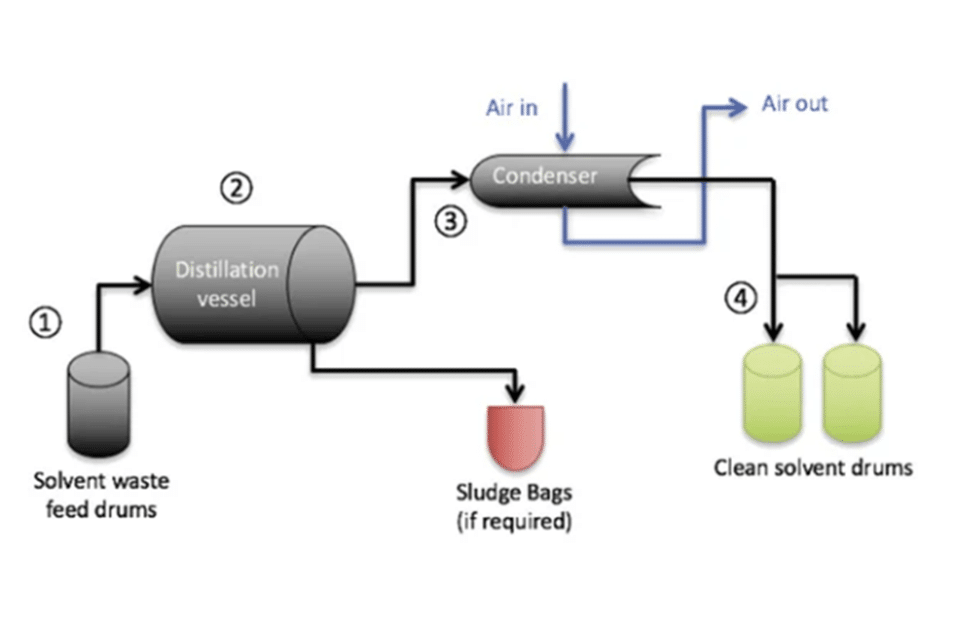
What are the different types of solvent recyclers?
Although solvent recyclers come in a variety of sizes, and can be configure with different options depending on the application, generally there are three types of solvent recyclers available:
- Batch-type solvent recyclers
- Continuous-flow solvent recyclers
- Distillation columns
Batch solvent recyclers
Fully automated distillation processes can be carried out every six hours, with treatment capacities of 30, 60, 120, 180 and 240 liters. This recycler requires very little supervision and maintenance, a simple periodic service of about 4 hours every 2,000 hours of operation. It can be used on demand and does not have to be constantly running.
Continuous-flow solvent recyclers
These operate virtually unsupervised, and can process from 15 to 375+ liters per hour, thanks to a fully automated solvent distillation process. Unlike the batch recycler, the continuous-flow recycler is designed to be practically always on. This means stable, efficient productivity every day. The continuous-flow solvent recycler is for companies with high and regular solvent usage.
Distillation columns
This fully-automated column chemical distillation system is designed specifically for high chemical purification applications, used within multiple industries. The system is designed to separate water, chemicals and/or contaminants from the chemical to be purified. It has a purification level of 99.9%.
Although solvent recyclers come in a variety of sizes, and can be configure with different options depending on the application, generally there are three types of solvent recyclers available:
- Batch-type solvent recyclers
- Continuous-flow solvent recyclers
- Distillation columns
Batch solvent recyclers
Fully automated distillation processes can be carried out every six hours, with treatment capacities of 30, 60, 120, 180 and 240 liters. This recycler requires very little supervision and maintenance, a simple periodic service of about 4 hours every 2,000 hours of operation. It can be used on demand and does not have to be constantly running.
Continuous-flow solvent recyclers
These operate virtually unsupervised, and can process from 15 to 375+ liters per hour, thanks to a fully automated solvent distillation process. Unlike the batch recycler, the continuous-flow recycler is designed to be practically always on. This means stable, efficient productivity every day. The continuous-flow solvent recycler is for companies with high and regular solvent usage.
Distillation columns
This fully-automated column chemical distillation system is designed specifically for high chemical purification applications, used within multiple industries. The system is designed to separate water, chemicals and/or contaminants from the chemical to be purified. It has a purification level of 99.9%.
What are the benefits of using solvent recyclers?
Purchasing a solvent recycler for your firm offers many benefits including:
- Large reduction in solvent purchasing costs
- Large reduction in used solvent disposal costs
- Reduction of the firm’s environmental footprint
- Reduction in solvent storage costs and space requirements
Reduction in solvent purchasing costs
Our solvent recyclers are generally able to recover 90%+ of the solvent from the dirty solvent mix. Since you will be recovering, and re-using the solvent up to 10x over, you will benefit from a dramatic decrease in your solvent purchasing costs. The more expensive the solvent you use in your operations, the greater the benefit.
Reduction in solvent disposal costs
Similarly, since you will be recycling and re-using your solvents multiple times, you will see a dramatic drop in your solvent disposal costs.
Reduction of your firm’s environmental footprint
Green marketing is all the rage lately. By using a solvent recycler to de-contaminate and re-use solvents, your firm can reduce its environmental impact, benefitting your company’s image while also benefitting the environment. A net positive for all stakeholders.
Reduction in solvent storage costs
Depending on the volume of solvent used in your operations, solvent storage can become expensive. Not only do you need to store all the unused solvent so that it is ready when your team needs it, you also need to store the used solvents while they await final disposal. In an operation with a high volume of solvent usage, the space requirements are non negligible. By using a solvent recycling system, you can reduce the space as well as the associated costs significantly.
Purchasing a solvent recycler for your firm offers many benefits including:
- Large reduction in solvent purchasing costs
- Large reduction in used solvent disposal costs
- Reduction of the firm’s environmental footprint
- Reduction in solvent storage costs and space requirements
Reduction in solvent purchasing costs
Our solvent recyclers are generally able to recover 90%+ of the solvent from the dirty solvent mix. Since you will be recovering, and re-using the solvent up to 10x over, you will benefit from a dramatic decrease in your solvent purchasing costs. The more expensive the solvent you use in your operations, the greater the benefit.
Reduction in solvent disposal costs
Similarly, since you will be recycling and re-using your solvents multiple times, you will see a dramatic drop in your solvent disposal costs.
Reduction of your firm’s environmental footprint
Green marketing is all the rage lately. By using a solvent recycler to de-contaminate and re-use solvents, your firm can reduce its environmental impact, benefitting your company’s image while also benefitting the environment. A net positive for all stakeholders.
Reduction in solvent storage costs
Depending on the volume of solvent used in your operations, solvent storage can become expensive. Not only do you need to store all the unused solvent so that it is ready when your team needs it, you also need to store the used solvents while they await final disposal. In an operation with a high volume of solvent usage, the space requirements are non negligible. By using a solvent recycling system, you can reduce the space as well as the associated costs significantly.
How much do solvent recyclers cost?
Although solvent recyclers aren’t cheap, they essentially pay for themselves, while also having a positive impact on your company’s environmental footprint.
The final price of the solvent recycler will depend on multiple factors including the machine’s capacity, the type of machine you choose, and the options you choose or need based on your particular solvent.
The price of the solvent recycling system can range from $12,000 for a small batch-type unit, to hundreds of thousands of dollars for large-scale distillation columns.
Although we can’t speak for other manufacturers, our solvent recyclers have a very quick payback period between two and a half and twelve months.
Operation and maintenance costs for solvent recyclers is pretty negligible.
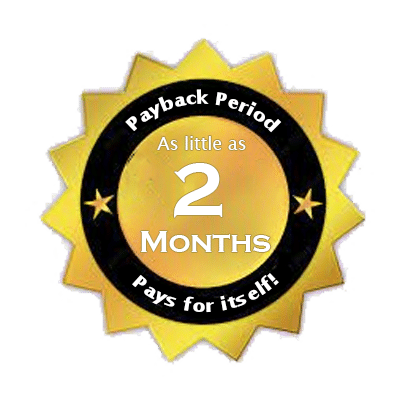
Save money and the environment!
Although solvent recyclers aren’t cheap, they essentially pay for themselves, while also having a positive impact on your company’s environmental footprint.
The final price of the solvent recycler will depend on multiple factors including the machine’s capacity, the type of machine you choose, and the options you choose or need based on your particular solvent.
The price of the solvent recycling system can range from $12,000 for a small batch-type unit, to hundreds of thousands of dollars for large-scale distillation columns.
Although we can’t speak for other manufacturers, our solvent recyclers have a very quick payback period between two and a half and twelve months.
Operation and maintenance costs for solvent recyclers is pretty negligible.
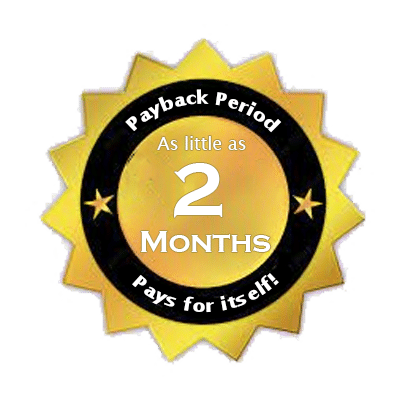
Save money and the environment!
Which industries use solvent recyclers?
Solvents are very commonly used in many industries. Solvents can be as cleaning agents, as intermediate compounds in the application of another product, or as a component in the formulation of many products.
Here is a non-exhaustive list of the industries using solvent recyclers:
- Automotive Manufacturing Industry
- Paint and Surface Treatment Industry
- Automotive Repair Industry
- Auto Body Repair Industry
- Food Processing Industry
- Pharmaceutical Industry
- Electronic Manufacturing Industry
- And many more!
Solvents are very commonly used in many industries. Solvents can be as cleaning agents, as intermediate compounds in the application of another product, or as a component in the formulation of many products.
Here is a non-exhaustive list of the industries using solvent recyclers:
- Automotive Manufacturing Industry
- Paint and Surface Treatment Industry
- Automotive Repair Industry
- Auto Body Repair Industry
- Food Processing Industry
- Pharmaceutical Industry
- Electronic Manufacturing Industry
- And many more!
Why choose IST Pure for your solvent recycler?
Choosing the right supplier for your solvent recycler is crucial to ensuring optimal performance and reliability now and in the future.
Here are a few reasons why IST Pure should be your top choice for your solvent recycler purchase:
- Over 40 years of manufacturing expertise
- Durable, high quality construction
- Track-record of constant innovation
- Multiple options to meet your specific use case
- Equipment certified by industry bodies
- Industry leading manufacturer warranty
- Customer-first focus
Choosing the right supplier for your solvent recycler is crucial to ensuring optimal performance and reliability now and in the future.
Here are a few reasons why IST Pure should be your top choice for your solvent recycler purchase:
- Over 40 years of manufacturing expertise
- Durable, high quality construction
- Track-record of constant innovation
- Multiple options to meet your specific use case
- Equipment certified by industry bodies
- Industry leading manufacturer warranty
- Customer-first focus